Inleiding tot siliciumcarbide
Siliciumcarbide (SiC) is een samengesteld halfgeleidermateriaal bestaande uit koolstof en silicium, dat een van de ideale materialen is voor het maken van apparaten met hoge temperaturen, hoge frequenties, hoog vermogen en hoge spanning. Vergeleken met het traditionele siliciummateriaal (Si) is de bandafstand van siliciumcarbide 3 keer die van silicium. De thermische geleidbaarheid is 4-5 keer die van silicium; de doorslagspanning is 8-10 keer die van silicium; de elektronische verzadigingsdrift is 2-3 keer die van silicium, wat voldoet aan de behoeften van de moderne industrie voor hoog vermogen, hoge spanning en hoge frequentie. Het wordt voornamelijk gebruikt voor de productie van elektronische componenten met hoge snelheid, hoge frequentie, hoog vermogen en lichtgevende componenten. De downstream toepassingsgebieden omvatten smart grid, nieuwe energievoertuigen, fotovoltaïsche windenergie, 5G-communicatie, enz. Siliciumcarbidediodes en MOSFET's zijn commercieel toegepast.
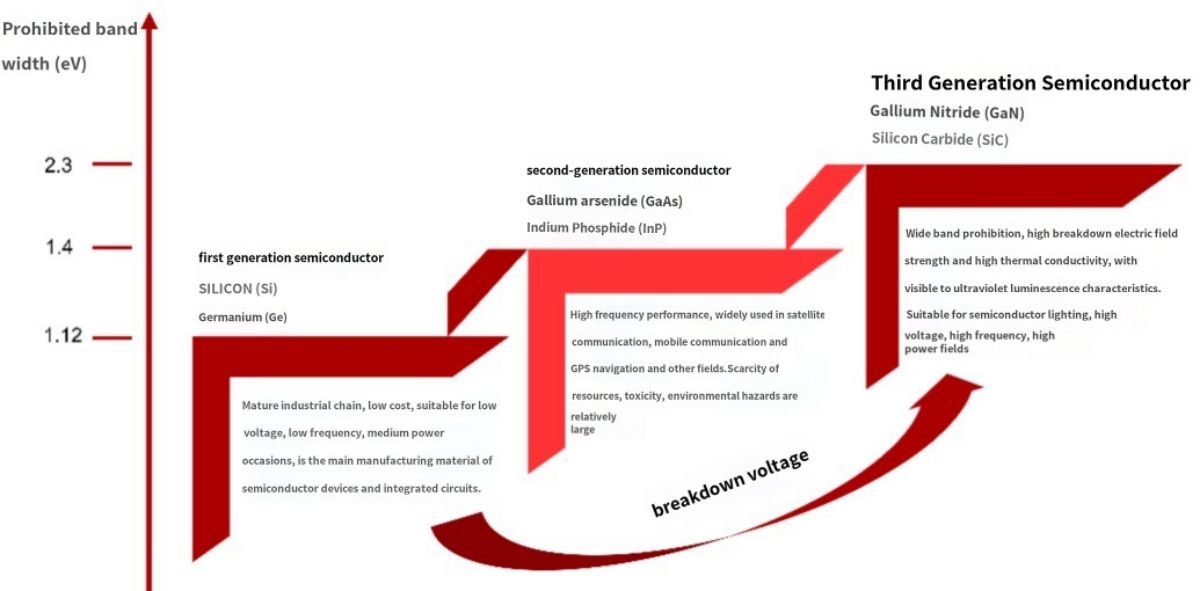
Hoge temperatuurbestendigheid. De bandgapbreedte van siliciumcarbide is 2-3 keer zo groot als die van silicium. De elektronen gaan moeilijk over bij hoge temperaturen en zijn bestand tegen hogere bedrijfstemperaturen. De thermische geleidbaarheid van siliciumcarbide is 4-5 keer zo groot als die van silicium, waardoor de warmteafvoer van het apparaat gemakkelijker wordt en de maximale bedrijfstemperatuur hoger ligt. De hoge temperatuurbestendigheid kan de vermogensdichtheid aanzienlijk verhogen en tegelijkertijd de eisen aan het koelsysteem verlagen, waardoor de terminal lichter en kleiner wordt.
Bestand tegen hoge druk. De elektrische veldsterkte van siliciumcarbide is 10 keer zo groot als die van silicium, dat hogere spanningen kan weerstaan en geschikter is voor hoogspanningsapparatuur.
Hoge frequentieweerstand. Siliciumcarbide heeft een verzadigde elektronendrift die twee keer zo hoog is als die van silicium, wat resulteert in de afwezigheid van stroomverlies tijdens het uitschakelen. Dit kan de schakelfrequentie van het apparaat effectief verbeteren en de miniaturisatie ervan realiseren.
Laag energieverlies. Vergeleken met siliciummateriaal heeft siliciumcarbide een zeer lage aan-weerstand en een laag aan-verlies. Tegelijkertijd vermindert de grote bandgap van siliciumcarbide de lekstroom en het vermogensverlies aanzienlijk. Bovendien heeft het siliciumcarbide geen last van naloopstroom tijdens het uitschakelen en is het schakelverlies laag.
Keten van de siliciumcarbide-industrie
Het omvat voornamelijk substraat, epitaxie, apparaatontwerp, productie, afdichting, enzovoort. Siliciumcarbide van het materiaal naar het halfgeleiderapparaat ondergaat monokristalgroei, ingot-slicing, epitaxiale groei, waferontwerp, productie, verpakking en andere processen. Na de synthese van siliciumcarbidepoeder wordt eerst de siliciumcarbide-ingot gemaakt, waarna het siliciumcarbidesubstraat wordt verkregen door middel van snijden, slijpen en polijsten, en de epitaxiale plaat wordt verkregen door middel van epitaxiale groei. De epitaxiale wafer wordt gemaakt van siliciumcarbide door middel van lithografie, etsen, ionenimplantatie, metaalpassivering en andere processen. De wafer wordt in een matrijs gesneden, het apparaat wordt verpakt en het apparaat wordt gecombineerd in een speciale behuizing en geassembleerd tot een module.
Stroomopwaarts van de industriële keten 1: substraat-kristalgroei is de kernschakel van het proces
Siliciumcarbidesubstraat vertegenwoordigt ongeveer 47% van de kosten van siliciumcarbideapparaten, de hoogste technische productiebarrières, de grootste waarde, en vormt de kern van de toekomstige grootschalige industrialisatie van SiC.
Vanuit het perspectief van verschillen in elektrochemische eigenschappen kunnen siliciumcarbidesubstraten worden onderverdeeld in geleidende substraten (weerstandsbereik 15-30 mΩ·cm) en semi-geïsoleerde substraten (weerstand hoger dan 105 Ω·cm). Deze twee soorten substraten worden gebruikt voor de productie van discrete apparaten, zoals vermogensapparaten en radiofrequentieapparaten, na epitaxiale groei. Semi-geïsoleerd siliciumcarbidesubstraat wordt voornamelijk gebruikt bij de productie van galliumnitride RF-apparaten, foto-elektrische apparaten, enzovoort. Door een epitaxiale laag te laten groeien op een semi-geïsoleerd SIC-substraat, wordt de epitaxiale SIC-plaat gevormd, die vervolgens kan worden verwerkt tot HEMT- of isonitride RF-apparaten. Geleidend siliciumcarbidesubstraat wordt voornamelijk gebruikt bij de productie van vermogensapparaten. Anders dan bij het traditionele productieproces van siliciumvoedingsapparaten, kan het siliciumcarbidevoedingsapparaat niet rechtstreeks op het siliciumcarbidesubstraat worden gemaakt. De epitaxiale laag van siliciumcarbide moet op het geleidende substraat worden aangebracht om de epitaxiale laag van siliciumcarbide te verkrijgen. De epitaxiale laag wordt vervaardigd op de Schottky-diode, MOSFET, IGBT en andere voedingsapparaten.
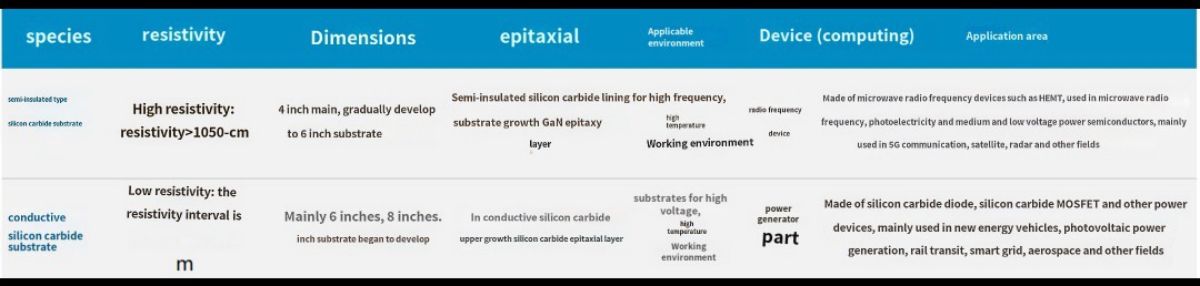
Siliciumcarbidepoeder werd gesynthetiseerd uit koolstofpoeder met een hoge zuiverheid en siliciumpoeder met een hoge zuiverheid. Verschillende siliciumcarbidestaven werden gekweekt onder een speciaal temperatuurveld. Vervolgens werd het siliciumcarbidesubstraat geproduceerd via meerdere verwerkingsprocessen. Het kernproces omvat:
Grondstofsynthese: Het siliciumpoeder met hoge zuiverheid en de toner worden gemengd volgens de formule en de reactie vindt plaats in de reactiekamer onder hoge temperaturen boven 2000 °C om siliciumcarbidedeeltjes te synthetiseren met een specifiek kristaltype en deeltjesgrootte. Vervolgens worden ze gebroken, gezeefd, gereinigd en andere processen uitgevoerd om te voldoen aan de eisen voor siliciumcarbidepoeder als grondstof met hoge zuiverheid.
Kristalgroei is het kernproces bij de productie van siliciumcarbidesubstraten en bepaalt de elektrische eigenschappen ervan. De belangrijkste methoden voor kristalgroei zijn momenteel fysische dampoverdracht (PVT), chemische dampdepositie bij hoge temperatuur (HT-CVD) en vloeistoffase-epitaxie (LPE). De PVT-methode is momenteel de meest gangbare methode voor commerciële groei van SiC-substraten, met de hoogste technische rijpheid en de meest gebruikte methode in de techniek.
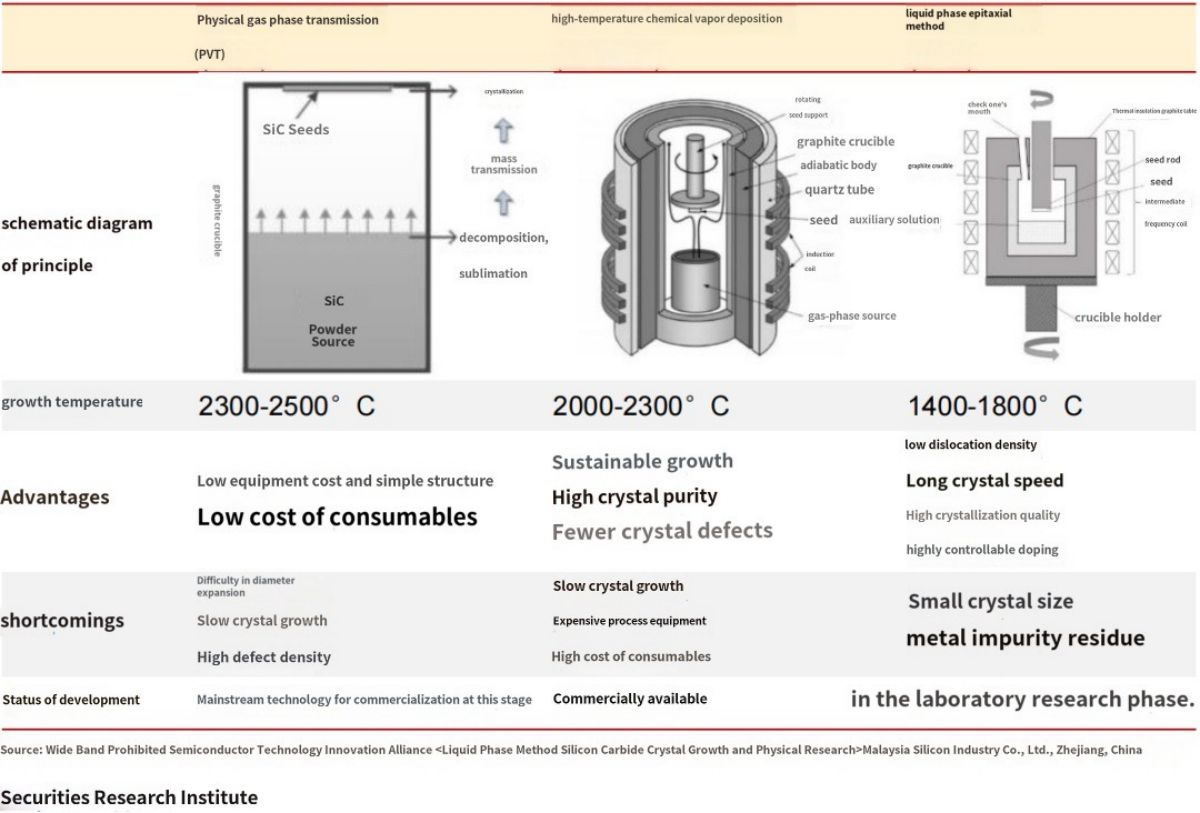
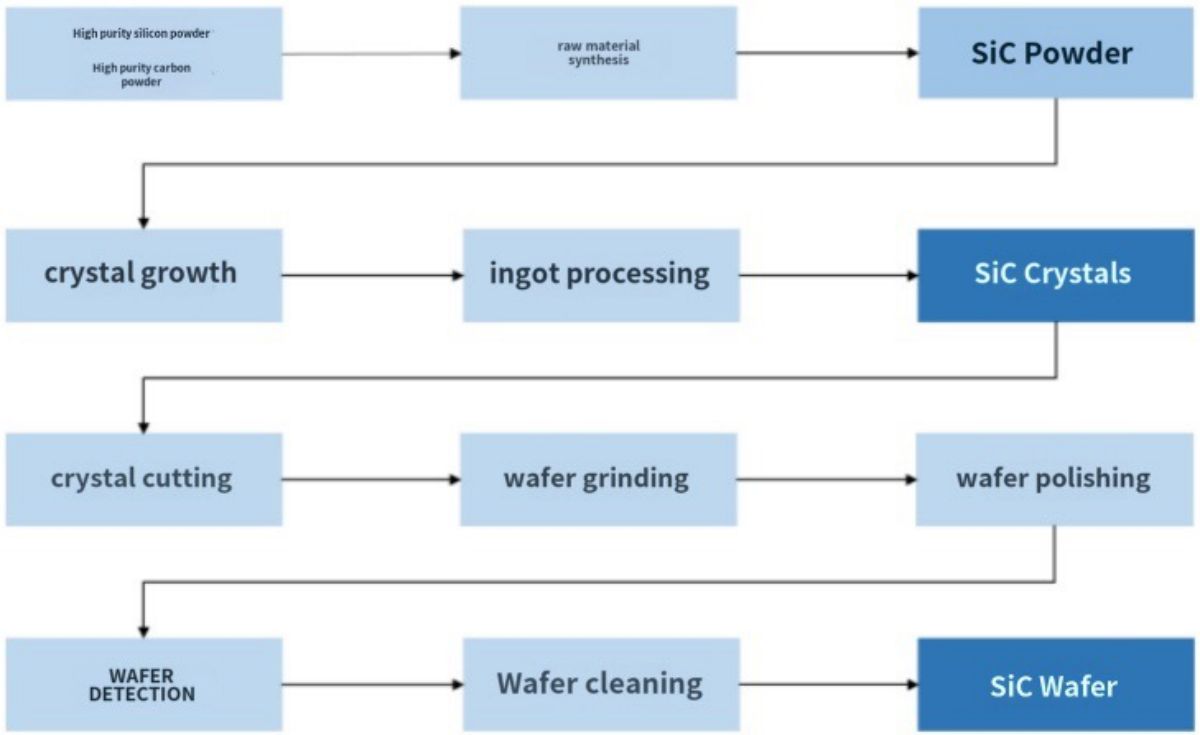
De voorbereiding van SiC-substraat is moeilijk, wat leidt tot de hoge prijs ervan
Temperatuurveldcontrole is moeilijk: Si-kristalstaafgroei vereist slechts 1500 ℃, terwijl SiC-kristalstaafgroei vereist is bij een hoge temperatuur boven 2000 ℃. Er zijn meer dan 250 SiC-isomeren, maar de belangrijkste 4H-SiC-kristalstructuur voor de productie van vermogenscomponenten zal, indien geen nauwkeurige controle, andere kristalstructuren verkrijgen. Bovendien bepaalt de temperatuurgradiënt in de smeltkroes de snelheid van SiC-sublimatieoverdracht en de rangschikking en groeiwijze van gasvormige atomen op het kristaloppervlak, wat de kristalgroeisnelheid en kristalkwaliteit beïnvloedt. Daarom is het noodzakelijk om een systematische technologie voor temperatuurveldcontrole te ontwikkelen. Vergeleken met Si-materialen is het verschil in SiC-productie ook terug te vinden in hogetemperatuurprocessen zoals ionenimplantatie bij hoge temperatuur, oxidatie bij hoge temperatuur, activering bij hoge temperatuur en het hard-mask-proces dat vereist is voor deze hogetemperatuurprocessen.
Langzame kristalgroei: de groeisnelheid van Si-kristalstaven kan 30-150 mm/u bereiken en de productie van een siliciumkristalstaaf van 1-3 m duurt slechts ongeveer 1 dag; SiC-kristalstaven met de PVT-methode als voorbeeld, de groeisnelheid is ongeveer 0,2-0,4 mm/u, het duurt 7 dagen om minder dan 3-6 cm te groeien, de groeisnelheid is minder dan 1% van het siliciummateriaal en de productiecapaciteit is uiterst beperkt.
Hoge productparameters en lage opbrengst: de kernparameters van SiC-substraat zijn onder meer de dichtheid van microtubuli, de dichtheid van dislocaties, de soortelijke weerstand, kromtrekken, de oppervlakteruwheid, enz. Het is een complex systeem om atomen in een gesloten hogetemperatuurkamer te ordenen en de kristalgroei te voltooien, terwijl de parameterindexen worden gecontroleerd.
Het materiaal heeft een hoge hardheid, hoge brosheid, lange snijtijd en hoge slijtage: de Mohs-hardheid van SiC van 9,25 is alleen te vergelijken met diamant, wat leidt tot een aanzienlijk hogere moeilijkheidsgraad van het snijden, slijpen en polijsten. Het duurt ongeveer 120 uur om 35-40 stukken uit een 3 cm dikke staaf te snijden. Bovendien zal de hoge brosheid van SiC de slijtage tijdens de waferverwerking verhogen en bedraagt de outputverhouding slechts ongeveer 60%.
Ontwikkelingstrend: Maattoename + prijsdaling
De wereldwijde SiC-markt met 6-inch volumeproductielijnen is aan het rijpen en toonaangevende bedrijven hebben de 8-inch markt betreden. Binnenlandse ontwikkelingsprojecten richten zich voornamelijk op 6-inch productielijnen. Hoewel de meeste binnenlandse bedrijven momenteel nog steeds gebaseerd zijn op 4-inch productielijnen, breidt de industrie zich geleidelijk uit naar 6-inch. Met de volwassenheid van de ondersteunende apparatuurtechnologie voor 6-inch, verbetert de binnenlandse SiC-substraattechnologie ook geleidelijk. De schaalvoordelen van grote productielijnen zullen worden weerspiegeld en de huidige binnenlandse 6-inch massaproductietijdkloof is teruggebracht tot 7 jaar. De grotere wafergrootte kan leiden tot een toename van het aantal afzonderlijke chips, een verbetering van de opbrengst en een vermindering van het aandeel randchips. Bovendien zullen de kosten van onderzoek en ontwikkeling en het opbrengstverlies op ongeveer 7% blijven, waardoor de waferbenutting verbetert.
Er zijn nog steeds veel moeilijkheden bij het ontwerpen van apparaten
De commercialisering van SiC-dioden verbetert geleidelijk. Momenteel hebben een aantal binnenlandse fabrikanten SiC SBD-producten ontwikkeld. SiC SBD-producten voor midden- en hoogspanning hebben een goede stabiliteit. In de OBC van voertuigen wordt SiC SBD + SI IGBT gebruikt om een stabiele stroomdichtheid te bereiken. Momenteel zijn er geen belemmeringen voor het patenteren van SiC SBD-producten in China en is de kloof met het buitenland klein.
SiC MOS kent nog steeds veel uitdagingen. Er gaapt nog steeds een kloof tussen SiC MOS en buitenlandse fabrikanten, en het relevante productieplatform is nog in ontwikkeling. Momenteel hebben ST, Infineon, Rohm en andere 600-1700V SiC MOS massaproductie bereikt en zijn ze met veel productiebedrijven overeengekomen en geleverd. Het huidige binnenlandse SiC MOS-ontwerp is in principe voltooid. Een aantal ontwerpfabrikanten werkt met fabs in de waferflowfase en de latere verificatie door klanten laat nog even op zich wachten. Het duurt dus nog lang voordat grootschalige commercialisering plaatsvindt.
Momenteel is de vlakke structuur de meest voorkomende keuze en in de toekomst zal het sleuftype veel worden gebruikt in de hogedruksector. Er zijn veel fabrikanten van SiC MOS-systemen met een vlakke structuur. De vlakke structuur is minder gemakkelijk te produceren in vergelijking met de groefstructuur, wat de stabiliteit van het werk beïnvloedt. De structuur heeft een breed toepassingsbereik onder 1200 V en is relatief eenvoudig te produceren, wat zowel de maakbaarheid als de kostenbeheersing ten goede komt. De groefstructuur heeft de voordelen van een extreem lage parasitaire inductantie, een hoge schakelsnelheid, een laag verlies en relatief hoge prestaties.
2--SiC wafer nieuws
Groei van de productie en verkoop van siliciumcarbide op de markt, let op structureel onevenwicht tussen vraag en aanbod
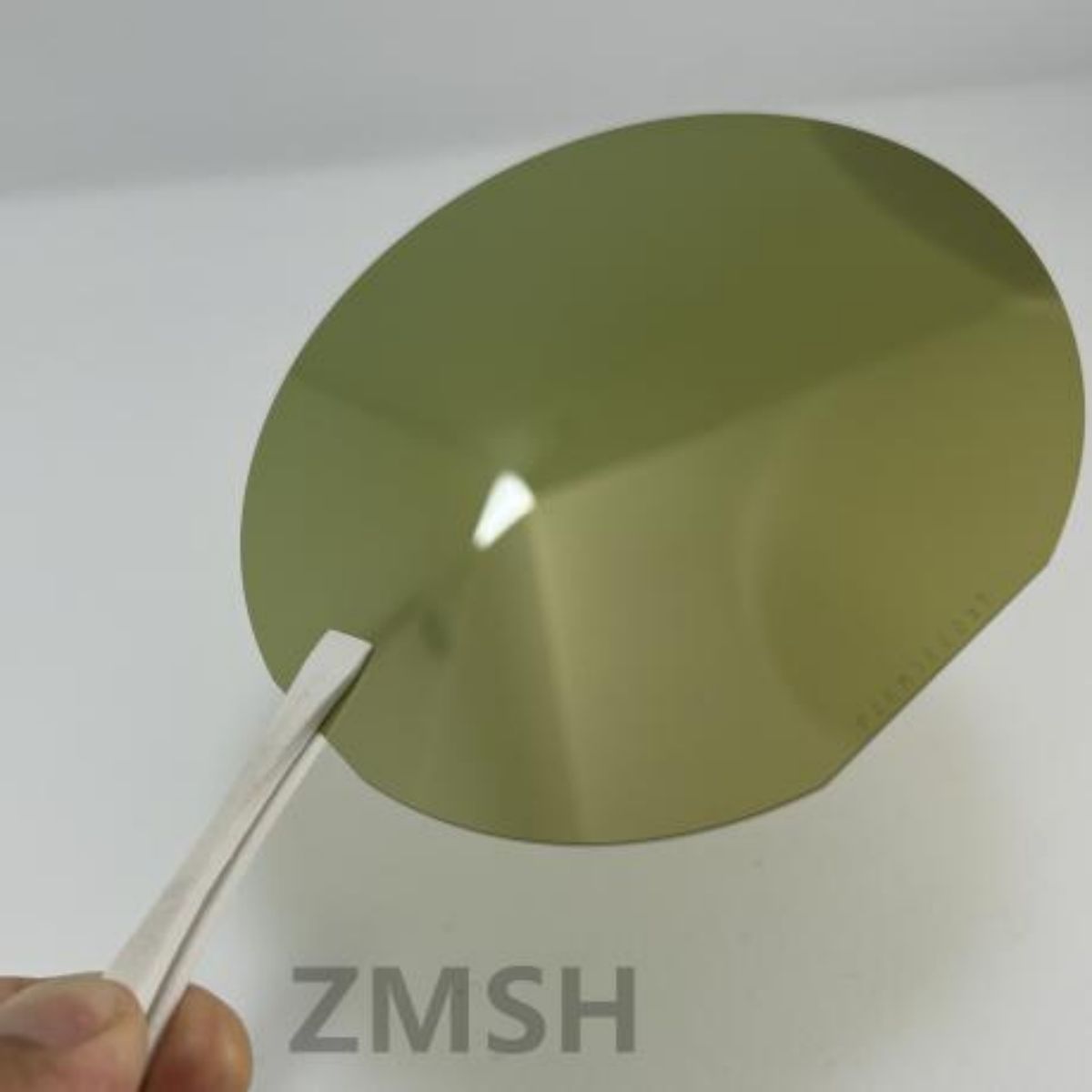
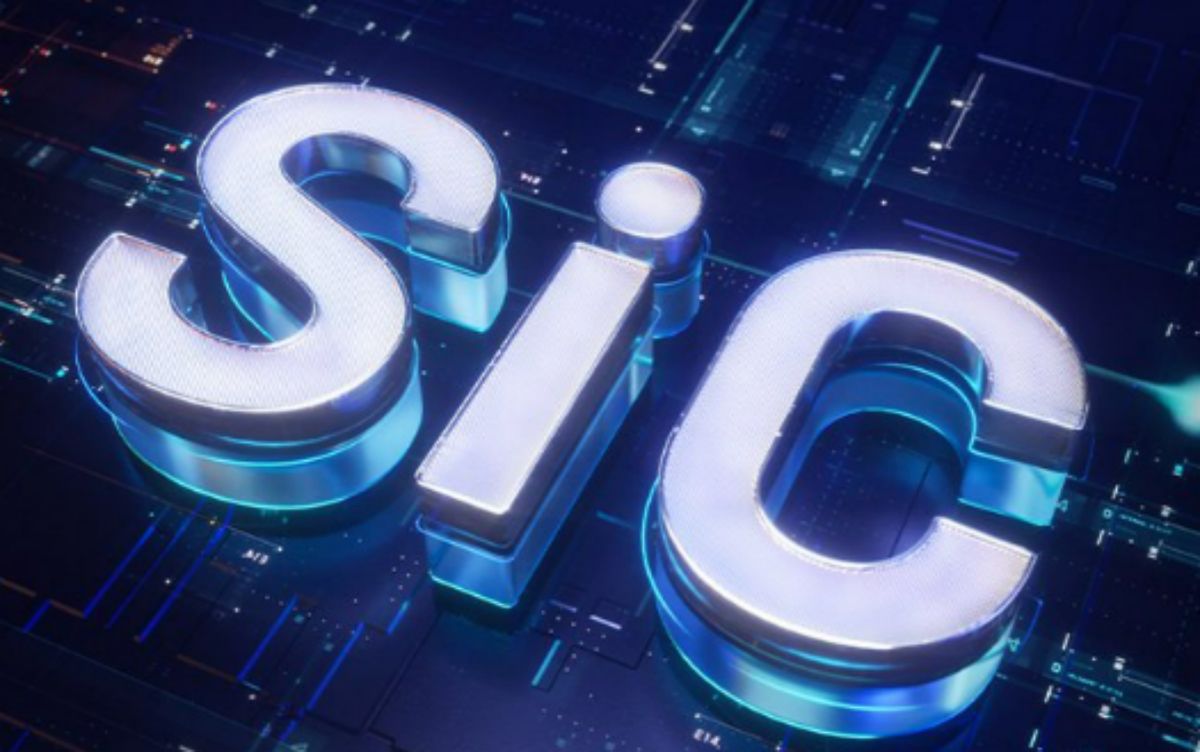
Met de snelle groei van de marktvraag naar hoogfrequente en hoogvermogenselektronica is de fysieke bottleneck van silicium-gebaseerde halfgeleiders geleidelijk aan prominent geworden en zijn de derde generatie halfgeleidermaterialen, siliciumcarbide (SiC), geleidelijk geïndustrialiseerd. Qua materiaalprestaties heeft siliciumcarbide een driemaal zo grote bandgap als siliciummateriaal, een tienmaal zo grote kritische elektrische veldsterkte en een driemaal zo grote thermische geleidbaarheid. Siliciumcarbide-apparaten zijn daarom geschikt voor toepassingen met hoge frequenties, hoge druk, hoge temperaturen en andere toepassingen, en dragen bij aan een hogere efficiëntie en vermogensdichtheid van vermogenselektronica.
Momenteel zijn SiC-diodes en SiC-MOSFET's geleidelijk aan op de markt gekomen en zijn er meer volwassen producten, waarbij SiC-diodes op grote schaal worden gebruikt in plaats van siliciumgebaseerde diodes in sommige sectoren omdat ze niet het voordeel van omgekeerde herstellading hebben; SiC-MOSFET wordt ook geleidelijk aan gebruikt in de automobielindustrie, energieopslag, laadpalen, fotovoltaïsche energie en andere sectoren; Op het gebied van automobieltoepassingen wordt de trend van modularisering steeds prominenter; de superieure prestaties van SiC moeten vertrouwen op geavanceerde verpakkingsprocessen om technisch gezien de toekomst te bereiken, met relatief volwassen schaalafdichting als mainstream, of met de ontwikkeling van kunststofafdichtingen, zijn de op maat gemaakte ontwikkelingskenmerken beter geschikt voor SiC-modules.
De prijs van siliciumcarbide daalt snel of onvoorstelbaar snel
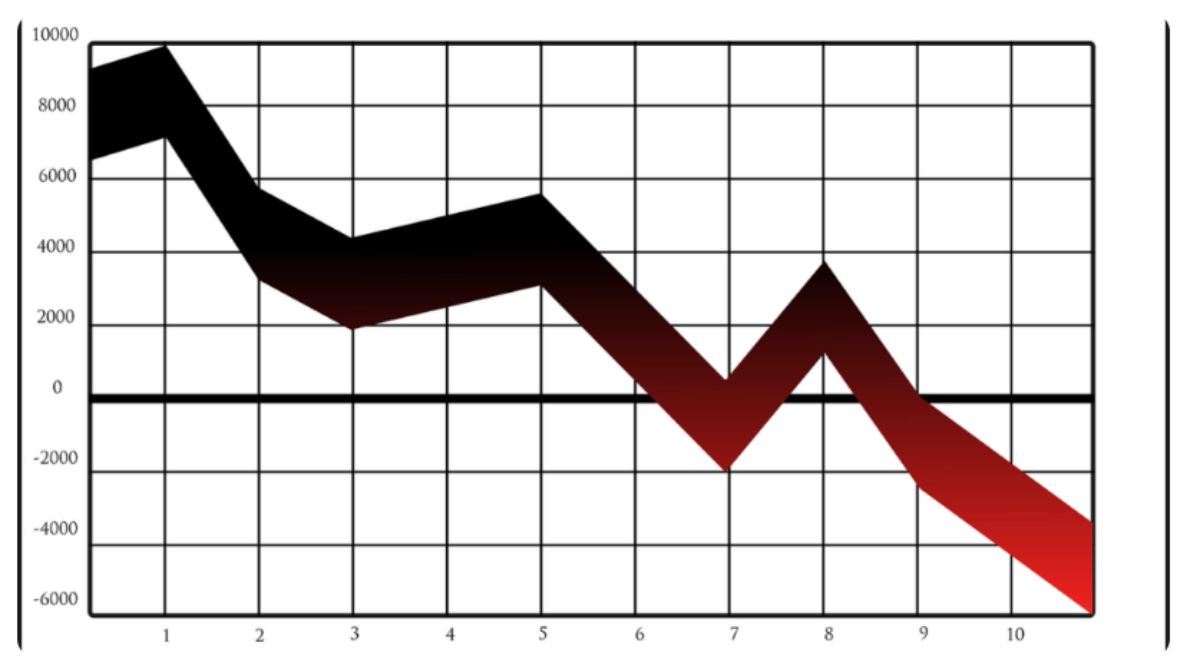
De toepassing van siliciumcarbidecomponenten wordt voornamelijk beperkt door de hoge kosten. De prijs van SiC MOSFET's onder hetzelfde niveau is vier keer hoger dan die van Si-gebaseerde IGBT's. Dit komt doordat het siliciumcarbideproces complex is, waarbij de groei van monokristallen en epitaxiale deeltjes niet alleen belastend is voor het milieu, maar ook traag is. Bovendien moet de verwerking van monokristallen tot het substraat een snij- en polijstproces doorlopen. Vanwege de materiaaleigenschappen en de onontwikkelde verwerkingstechnologie bedraagt de opbrengst van binnenlands substraat minder dan 50%. Verschillende factoren leiden tot hoge substraat- en epitaxiale prijzen.
De kostensamenstelling van siliciumcarbide- en siliciumgebaseerde apparaten is echter diametraal tegengesteld: de substraat- en epitaxiale kosten van het frontkanaal vertegenwoordigen respectievelijk 47% en 23% van het totale apparaat, in totaal ongeveer 70%. Het ontwerp, de productie en de afdichtingsverbindingen van het backkanaal vertegenwoordigen slechts 30%. De productiekosten van siliciumgebaseerde apparaten zijn voornamelijk geconcentreerd in de waferproductie van het backkanaal (ongeveer 50%) en de substraatkosten vertegenwoordigen slechts 7%. Het fenomeen van de waardeketen van de siliciumcarbide-industrie op zijn kop betekent dat upstream substraat-epitaxiefabrikanten het belangrijkste recht van spreken hebben, wat de sleutel is tot de structuur van binnenlandse en buitenlandse ondernemingen.
Vanuit dynamisch oogpunt op de markt is het verlagen van de siliciumcarbidekosten, naast het verbeteren van het siliciumcarbide lange kristal- en snijproces, ook een manier om de wafergrootte te vergroten. Dit is ook de meest beproefde methode voor de ontwikkeling van halfgeleiders in het verleden. Gegevens van Wolfspeed tonen aan dat de upgrade van siliciumcarbidesubstraten van 6 inch naar 8 inch de productie van gekwalificeerde chips met 80%-90% kan verhogen en de opbrengst kan verbeteren. Dit kan de gecombineerde kosten per eenheid met 50% verlagen.
2023 staat bekend als het "eerste jaar van 8-inch SiC". Dit jaar versnellen binnenlandse en buitenlandse fabrikanten van siliciumcarbide de aanleg van 8-inch siliciumcarbide, zoals Wolfspeed de gekke investering van 14,55 miljard Amerikaanse dollar in de uitbreiding van de siliciumcarbideproductie. Een belangrijk onderdeel hiervan is de bouw van een fabriek voor de productie van 8-inch SiC-substraten. Om de toekomstige levering van 200 mm SiC-blank metaal aan een aantal bedrijven te garanderen, hebben Domestic Tianyue Advanced en Tianke Heda ook langetermijnovereenkomsten gesloten met Infineon om in de toekomst 8-inch siliciumcarbidesubstraten te leveren.
Vanaf dit jaar zal siliciumcarbide versnellen van 6 inch naar 8 inch. Wolfspeed verwacht dat de kosten per chip van een 8 inch substraat in 2024 met meer dan 60% zullen dalen ten opzichte van de kosten per chip van een 6 inch substraat in 2022. Deze kostendaling zal de toepassingsmarkt verder openen, zo blijkt uit onderzoeksgegevens van Ji Bond Consulting. Het huidige marktaandeel van 8 inch producten bedraagt minder dan 2% en zal naar verwachting groeien tot ongeveer 15% in 2026.
In feite kan de snelheid van de daling van de prijs van siliciumcarbidesubstraat de verbeelding van veel mensen overtreffen, het huidige marktaanbod van 6-inch substraat is 4000-5000 yuan/stuk, vergeleken met het begin van het jaar is het veel gedaald, naar verwachting zal het volgend jaar onder de 4000 yuan dalen, het is vermeldenswaard dat sommige fabrikanten om de eerste markt te krijgen, de verkoopprijs hebben verlaagd naar de kostenlijn eronder, het model van de prijsoorlog hebben geopend, voornamelijk geconcentreerd in het siliciumcarbidesubstraataanbod is relatief voldoende geweest in het laagspanningsveld, binnenlandse en buitenlandse fabrikanten breiden agressief hun productiecapaciteit uit, of laten het overaanbod van siliciumcarbidesubstraat eerder dan gedacht.
Plaatsingstijd: 19-01-2024